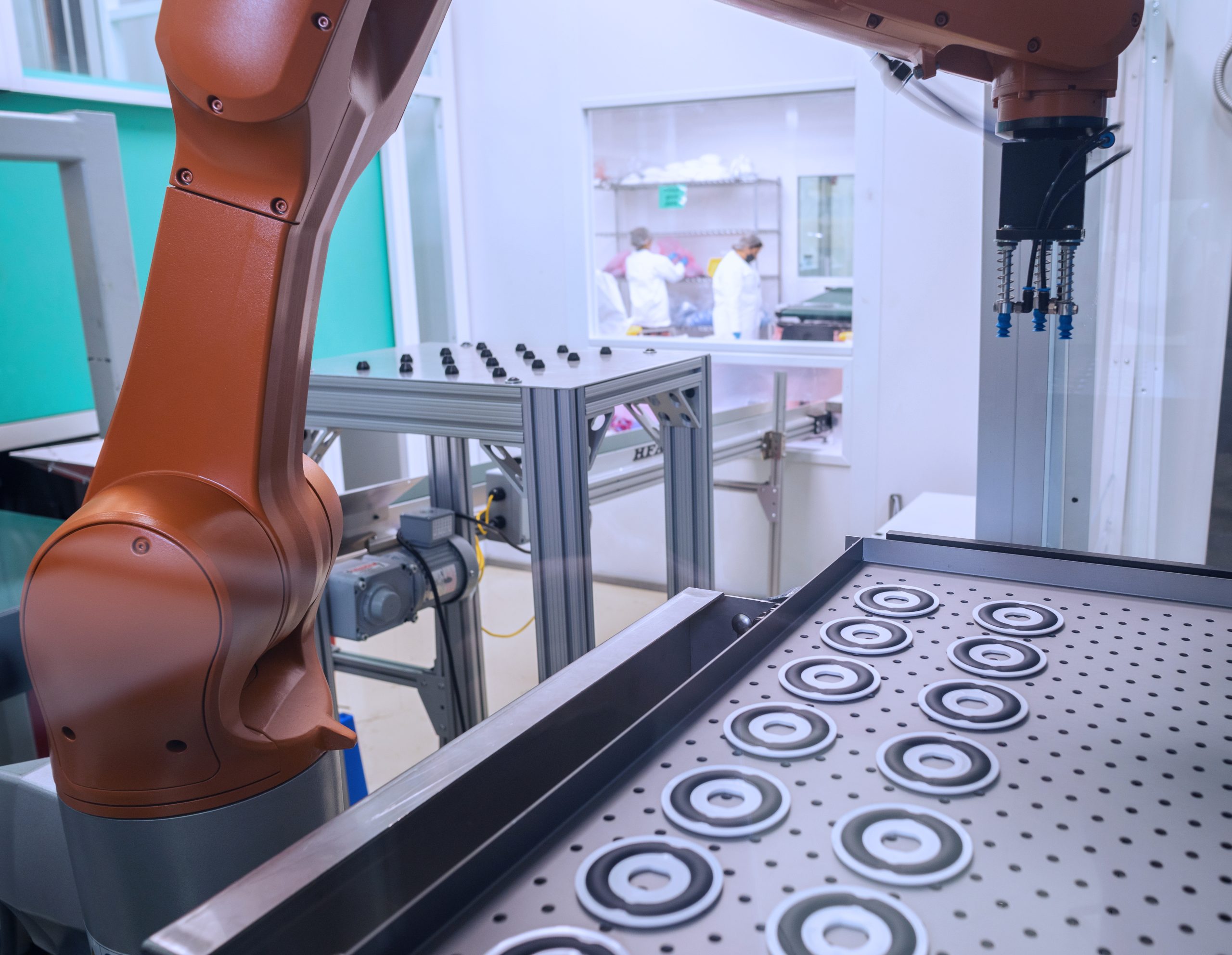
Value-Added Secondary Processes
At SIMTEC Silicone Parts, we offer in-line post-molding secondary processes that eliminate the need for independent secondary operations, add value and increase productivity for our customers.
Our post-molding services are fully automated and performed within the same process, immediately after the components are robotically removed from their molds. Examples of these secondary processes include:
Post-Molding Value Added Operations Include:
- Slitting: A customized slitting station, located with the molding cell, slits valves and other LSR components consistently and with precision accuracy. Performing a uniform and exact slitting operation can be challenging especially when LSR is the material due to its elasticity and flexibility characteristics.
- Laser Making: We laser mark your Liquid Silicone Rubber (LSR) parts with specific product identifiers, such as product or serial numbers.
- Packaging: Using customized automation, parts are individually packaged and cell packed, immediately after molding, providing added protection from airborne particles.
Inline Value-Added Secondary Processes
Our customized fixtures precisely place and index the molded parts to ensure exact positioning. The result is precise alignment of parts and consistent, accurate execution.
Contact SIMTEC To Discuss Your Project Today
With design flexibility, advanced technology and exceptional quality, there’s no better partner to manufacture your high volume Liquid Silicone components than SIMTEC. Contact us today to discuss your requirements.